

Through these optimizations, this study obtained an optimum combination of design parameters and fignificantly reduced the noise generated by rear-glass section.Ĭhoi, S. Each step is carried out with FEA and validated by sealant penetration experiments. The optimal design comprises of two steps: sealant injections shape optimization and rear-glass joint parameter optimization. The design maximized the sealant penetration length, which is a parameter that majorly affects noise.
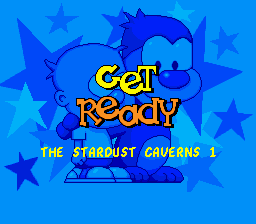
In addition, this study created an optimal design with Design of Experiments (DOE) of the rear-glass joint. The sealant penetration length, panelmolding distance, and sealant width are the parameters affecting noise generation. Based on these two approaches, this study confirms that S/R noises generate through the contact between bottom side of molding and BIW. This study uses, two approaches, experimental and numerical approaches, to define the cause of S/R noise at the rear-glass section. Among them, the rear-glass joint is a major source for vehicle interior noise, and can cause S/R noises under a variety of environmental and driving conditions. Generally, people detect S/R noises on automotive interior parts, brake system, suspension, Body in White (BIW), etc. Ever since vehicle noise, vibration, and harshness (NVH) reduction technology made dramatic improvements, vehicle interior noises represented by Squeak and Rattle (S/R) becomes an ever more important factor to improve the emotional quality of vehicles.
